Aluminum Vacuum Innovation
Over 30 years ago, Atlas Technologies pioneered the use of aluminum for UHV and XHV applications. Then we perfected our bimetal bonding techniques and developed Atlas Bimetal CF Flanges. This allows our customers to take advantage of the many favorable qualities of aluminum for vacuum and convert large portions of their systems to this superior metal.
Advanced Joining:
One of the challenges of using aluminum for UHV/XHV chambers, is that aluminum is not suitable for a CF knife edge. Through our advanced bonding techniques, we efficiently join aluminum to stainless or titanium, allowing a durable CF knife edge on flanges that can then be welded to the high-performance aluminum chamber.
Over the last three decades Atlas Technologies has concentrated on developing methods and processes specifically intended for bonding dissimilar metals for use in Ultrahigh Vacuum (UHV). Atlas has received patents on several applications related to this technology
Advanced Surface Treatments:
Atlas’ mirror-like Emissivac aluminum surface limits thermal emissivity and improves vacuum performance by reducing surface roughness and eliminating polishing compounds with poor vacuum properties. The Emissivac surface is created by hand polishing without the use of any potentially contaminating polishing compounds. It is a time and labor-intensive process that can significantly increase costs so should be used only when resulting performance characteristics are critical for your project.
Consider the superior vacuum properties of aluminum:
- Minimal carbon and hydrogen content: With seven orders of magnitude less hydrogen and far less carbon contamination than stainless steel, aluminum is ideal for UHV and XHV applications. Atlas UHV aluminum chambers feature a thin but dense aluminum oxide coating that reduces diffusion and desorption of HV and UHV contaminates.
- Efficient bake outs and unmatched thermal performance: 10x the thermal conductivity and 21x the thermal diffusivity of stainless steel makes aluminum an ideal vacuum material. The extremely low thermal emissivity rates facilitate a rapid and uniform bake-out at 150°C.
- Outgassing rates of less than 1 x 10-13 Torr liter/sec cm2: suitable for extreme high vacuum.
- High resistance to a variety of chemicals: Aluminum is naturally resistant to many chemicals and can also be anodized for additional electrical or chemical control
- Low nuclear activation for less residual radiation: Aluminum has a short neutron activated half-life – mere hours as compared to thousands of years for SST. This offers huge disposal savings and a priceless reduction in potential exposure to personnel.
- Completely non-magnetic: Aluminum is essentially magnetically transparent (non-magnetic). An aluminum UHV chamber’s low magnetic permeability offers no measurable disruption to electron and ion optics.
- High vibration dampening / low Young’s modulus: With a low Youngs’ modulus (69GPa) of elasticity (1/3 that of stainless steel, 207GPa) aluminum offers outstanding vibration dampening, making it the material of choice for precision synchrotron, semiconductor, and physics applications where excess vibration can have disastrous consequences.
- Improved bottom line: Lighter in weight than stainless, aluminum is easier to manage and less costly to ship. Reduced material costs, faster machinability and lower bakeout and pumping costs make it even more affordable.
Aluminum’s Extreme Vacuum Performance
All our aluminum chambers are processed per Atlas specification AVSP-08. All surfaces are cleaned and detailed to facilitate the formation of a dense oxide passivation layer through the conversion of hydroxides into stable oxide molecules. The resulting surface inhibits the diffusion of other contaminants, further reducing pumping requirements. Faster pumping equates to smaller and less expensive pumps.
Fluorine gas is a common cleaning agent in aluminum chambers. Atlas’ AVSP-08 process forms a dense protective oxide layer that makes our aluminum chambers far more corrosion resistant than their stainless steel equivalents. These surfaces can be further protected from halogens by producing even thicker and harder oxide layers through an electrolytic anodizing process.
With 10x the thermal conductivity and 21x the thermal diffusivity of stainless steel, the extremely low thermal emissivity rates cause our aluminum chambers to bake-out quickly and evenly. The surface properties of aluminum allow full bake-out at 150°C — much lower than stainless. Aluminum chambers heat up quickly and uniformly, bake-outs are faster and more complete with significantly reduced cycle times.
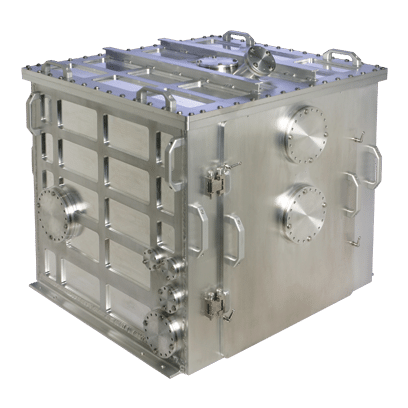
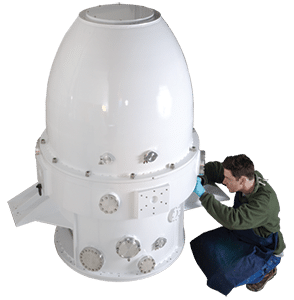
With a low Young’s’ modulus (69GPa) of elasticity (1/3 that of stainless steel, 207GPa) aluminum offers outstanding vibration dampening, making it the material of choice for precision synchrotron, semiconductor, and physics applications where excess vibration can have disastrous consequences.
At about 1/3 the weight of stainless steel, even if chamber walls need to be slightly thicker for strength, aluminum chambers are significantly lighter and require less expensive support structures. The cost burden associated with excess weight begins when the raw materials are handled and progresses throughout the manufacturing process. It affects all production steps, including shipping, installation, and even the architectural engineering and construction of the environment surrounding the chamber. The reduced weight also translates into reduced shipping costs and faster installation times.
No matter the size or shape of your chamber design, we can build it in aluminum for increased performance and reliability.
HOW CAN WE ASSIST IN YOUR PRODUCT DEVELOPMENT NEEDS?
From our first custom aluminum vacuum chamber, to our recent niobium to stainless steel fittings for satellite delivery rockets, to our standard bimetal and titanium flanges and fittings, Atlas Technologies has been the solution of choice for mission critical projects around the world. Whether you have a simple sketch, a full-fledged design, or just need a handful of our US-manufactured bimetal products, we can help.