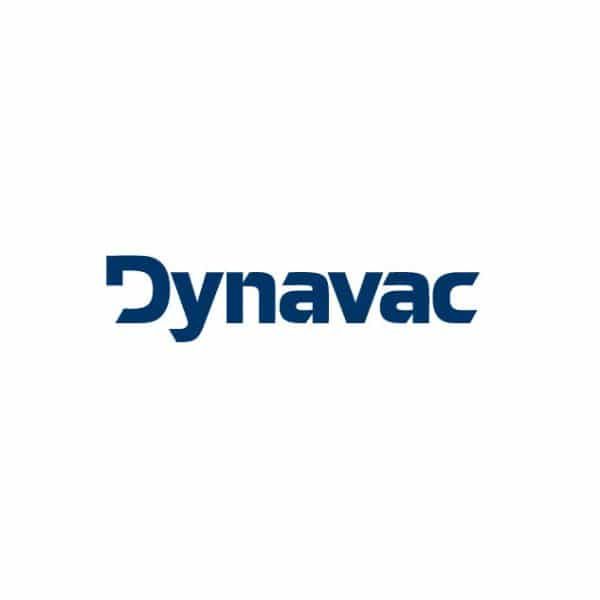
Our customers at Dynavac were crucial participants in a compelling project for NASA’s Magnetospheric Multiscale Mission at the Goddard Space Center.
The Solar Terrestrial Probes mission were scheduled to fly four identically instrumented satellites to investigate how the sun and Earth’s magnetic fields transfer energy from one to the other. This transfer, called Magnetic Reconnection, affects space weather and by studying it, scientists at NASA gained the ability to observe how this process affects systems like communications networks, GPS navigation, and power grids back on Earth.
Dynavac, an industry leader in the design and manufacture of thermal vacuum systems, supplied the project with aluminum cryopanel assemblies that allowed for thermal isolation of the satellites while they went through space simulation exercises in the lab prior to their journey in space. Each assembly was comprised of multiple panels joined together to form a thermally controlled and uniform test area. Aluminum extrusion was welded to each of the panels in a serpentine pattern which ultimately connected to stainless steel lines that delivered the liquids and gases to the assembly.
Dynavac uses Atlas ATCR fittings to provide a compatible, demountable transition from the aluminum lines to their stainless-steel counterparts. Atlas has supplied Dynavac with thousands of ATCR fittings for the manufacture of their equipment.
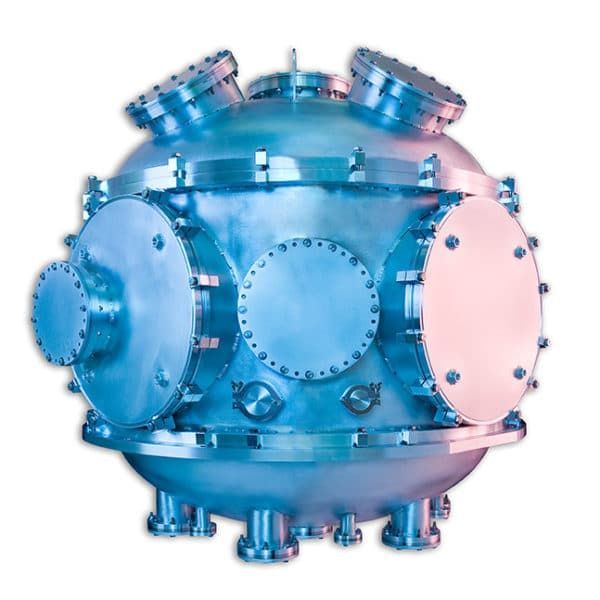
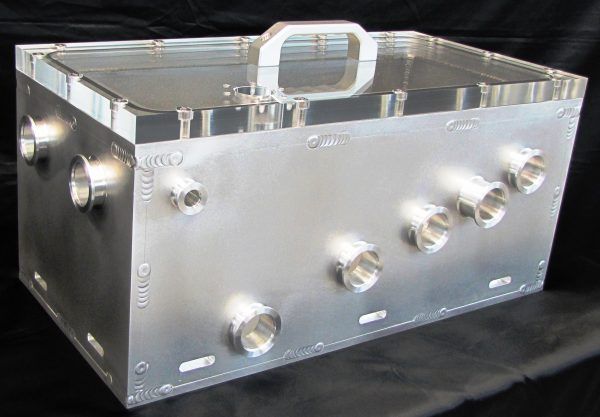
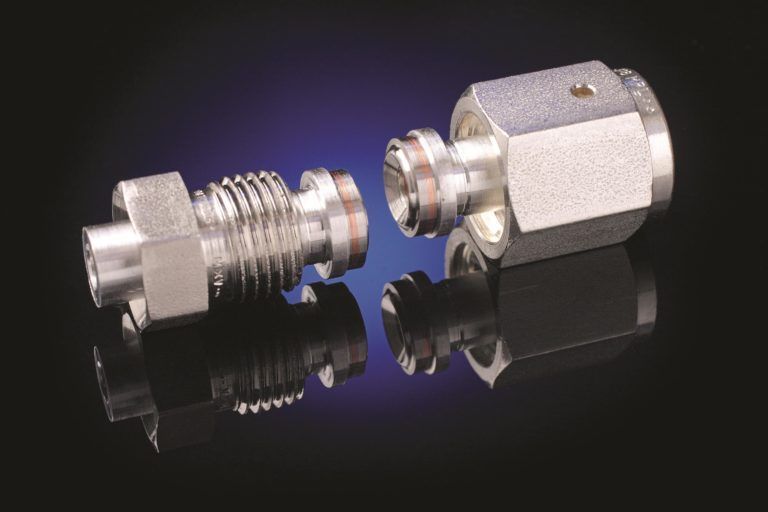
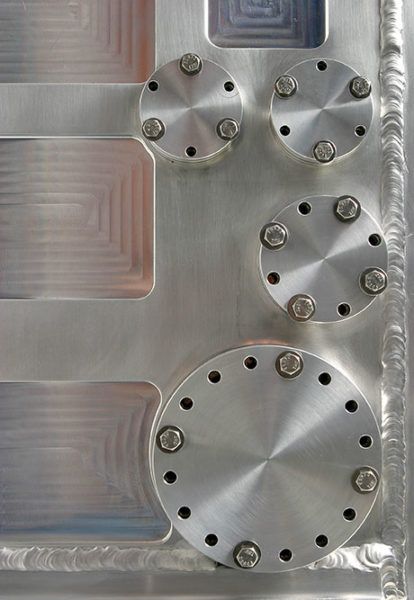
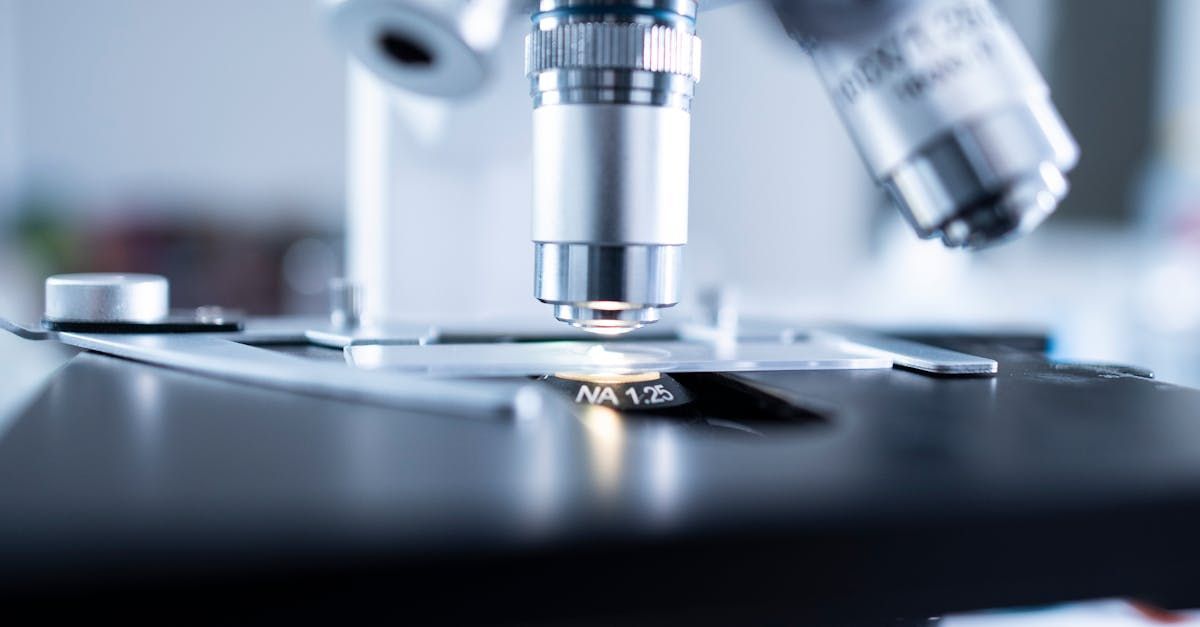
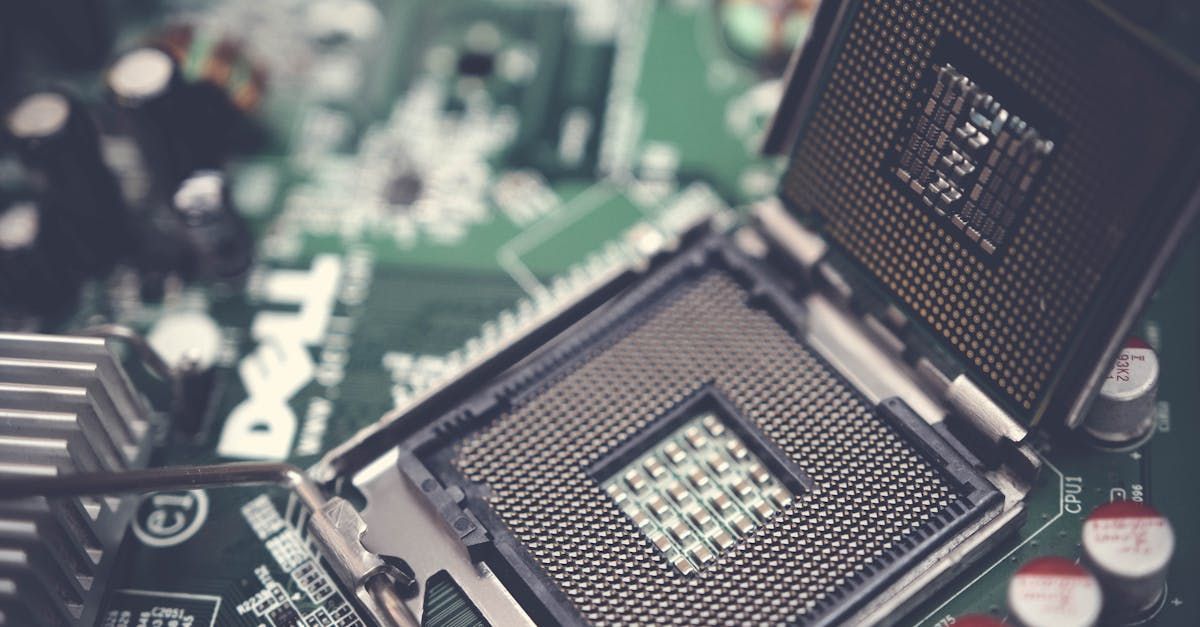