Rocket engines reach such high temperatures that they melt most metals, yet some metals are too expensive to use exclusively. Bimetal components offer an effective solution.
Whether designed for low earth orbit, geostationary orbit, or open space, spacecraft must maneuver flawlessly and operate repeatedly in one of the harshest environments. Therefore, each component must interact with precision, provide leak-free operation, and support system longevity.
As our aerospace customers continually innovate and launch ever more sophisticated space craft, bimetal plays a critical role in their upgraded designs. Here are three reasons it makes sense.
HIGH-TEMPERATURE OPERATION
Satellites and spacecraft use a variety of chemical propulsion systems to provide maneuverability. Engine designs must incorporate materials that can withstand the heat generated by the thrusters without failing. For example, the use of niobium alloy as part of the thruster’s nozzle, where temperatures can reach 2000℉, must connect with the stainless-steel components used in the fabrication of other rocket engine parts.
Niobium can be expensive—more expensive than sterling silver—and offers a number of benefits to users, including oxidation and corrosion resistant properties, and a melting temperature of 4,491℉ for use in high pressure and high temperature applications. Using bimetal components combines the advantages of both metals—the heat and chemical resistance of niobium for example, and the lighter weight and/or lower cost
of stainless steel or aluminum—resulting in a more resilient, less costly, and longer-lived system.
Although bimetallic components can be joined using one of two primary operations (explosion bonding or diffusion bonding), most
aerospace components are explosion bonded at this time.
PRECISION FABRICATION
Stainless steel cannot be welded directly to niobium. The use of a conventional weld would result in a fragile, glass-like interconnection joint that would easily shatter under a high vibration and shock operation. Atlas Technologies has helped rocket engine designers develop new solutions through specially bonded metals and precision machining techniques to provide a bimetallic transition for such critical joints.
Our fully weldable dissimilar metal transitions allow us to help customers with specific requirements including light weight, ability to handle high temperatures, chemical resistance, and more.
EXTENDED LIFE CYCLES
Bimetallic joints are solid-state joints with long-term reliability that require no servicing, unlike joints utilizing adhesives, bolts, and elastomeric seals. This is especially beneficial in space where it is challenging to replace a component. These hermetic bimetallic joints enable engineers to reliably transition from one metal to another with metallurgically bonded joints.
For OEMs and end users, these robust dissimilar metal joints can be produced with a wide variety of metal combinations such as aluminum/titanium, stainless/titanium, copper/titanium, copper/aluminum, niobium/stainless, and many more.
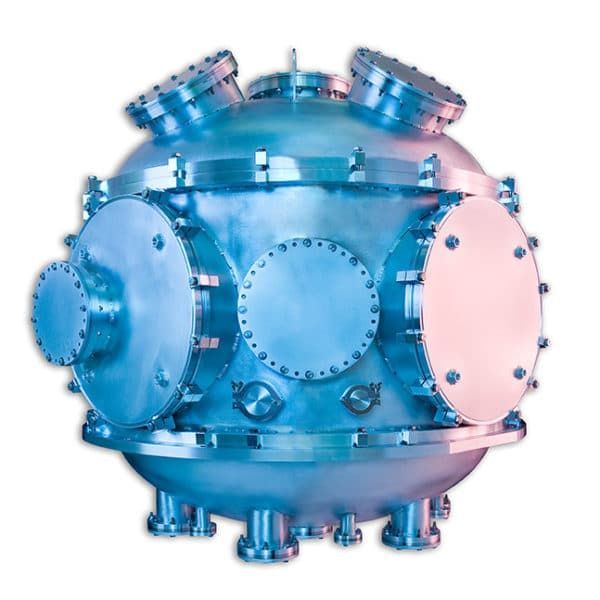
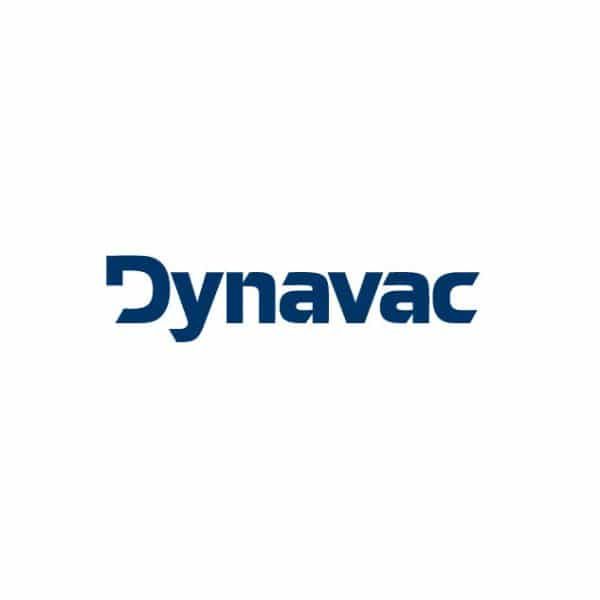
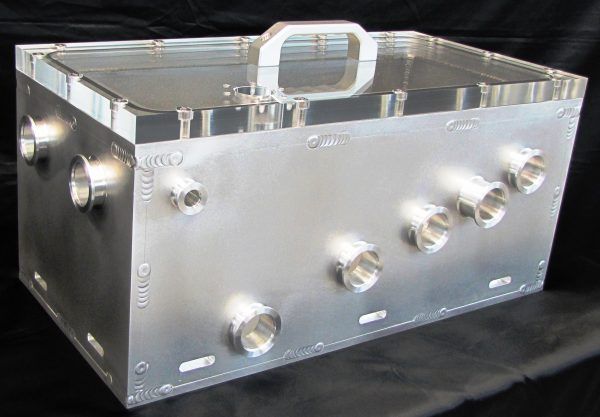
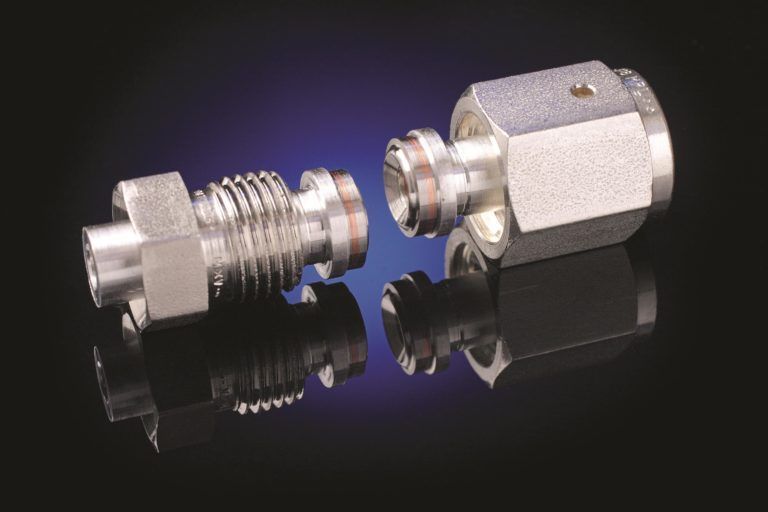
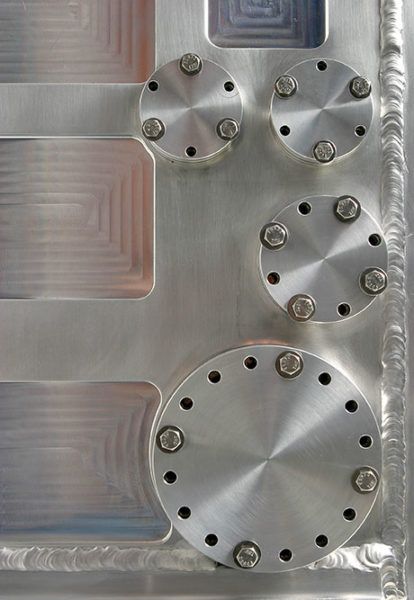
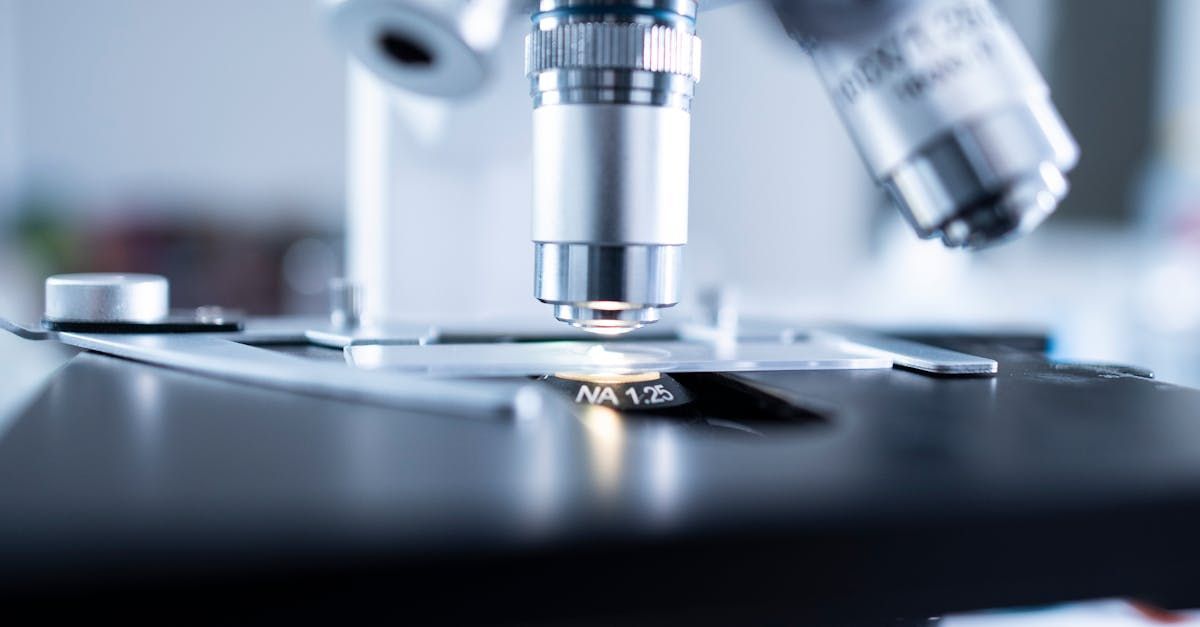
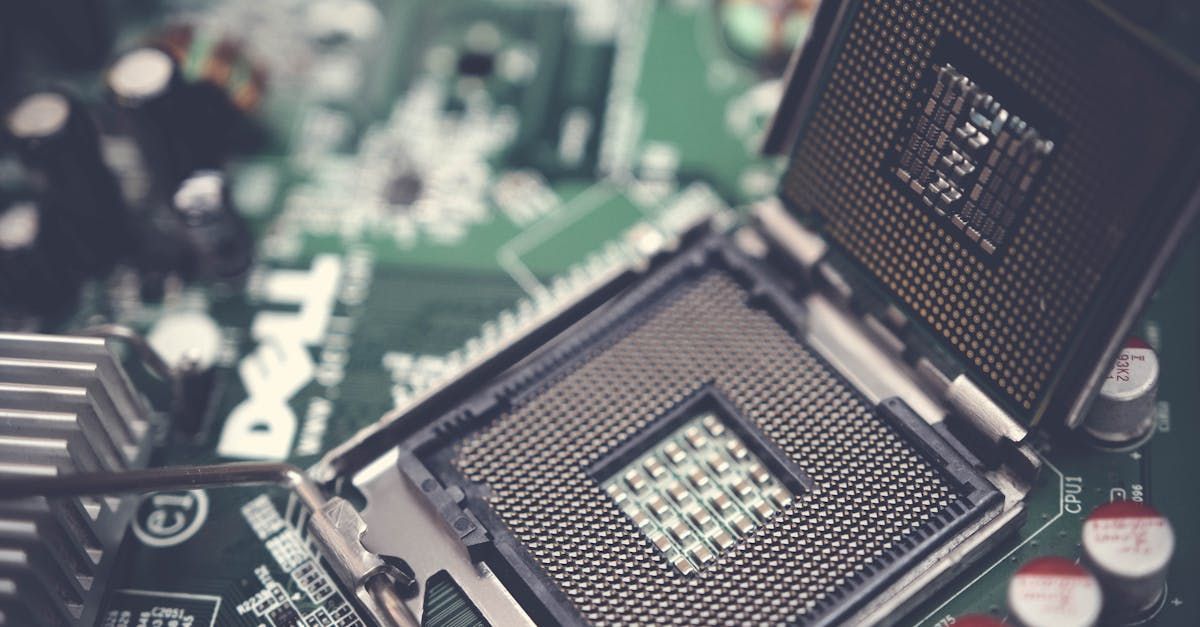
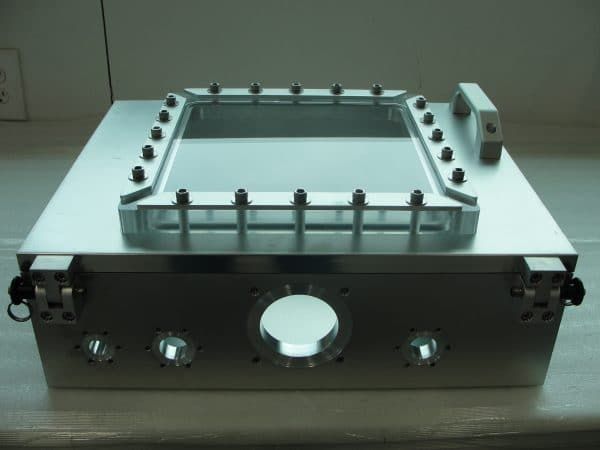